Where Foresight Meets Follow Through
TRC is a leading, global consulting, engineering and construction management firm that provides environmentally focused and digitally powered solutions across our key markets.
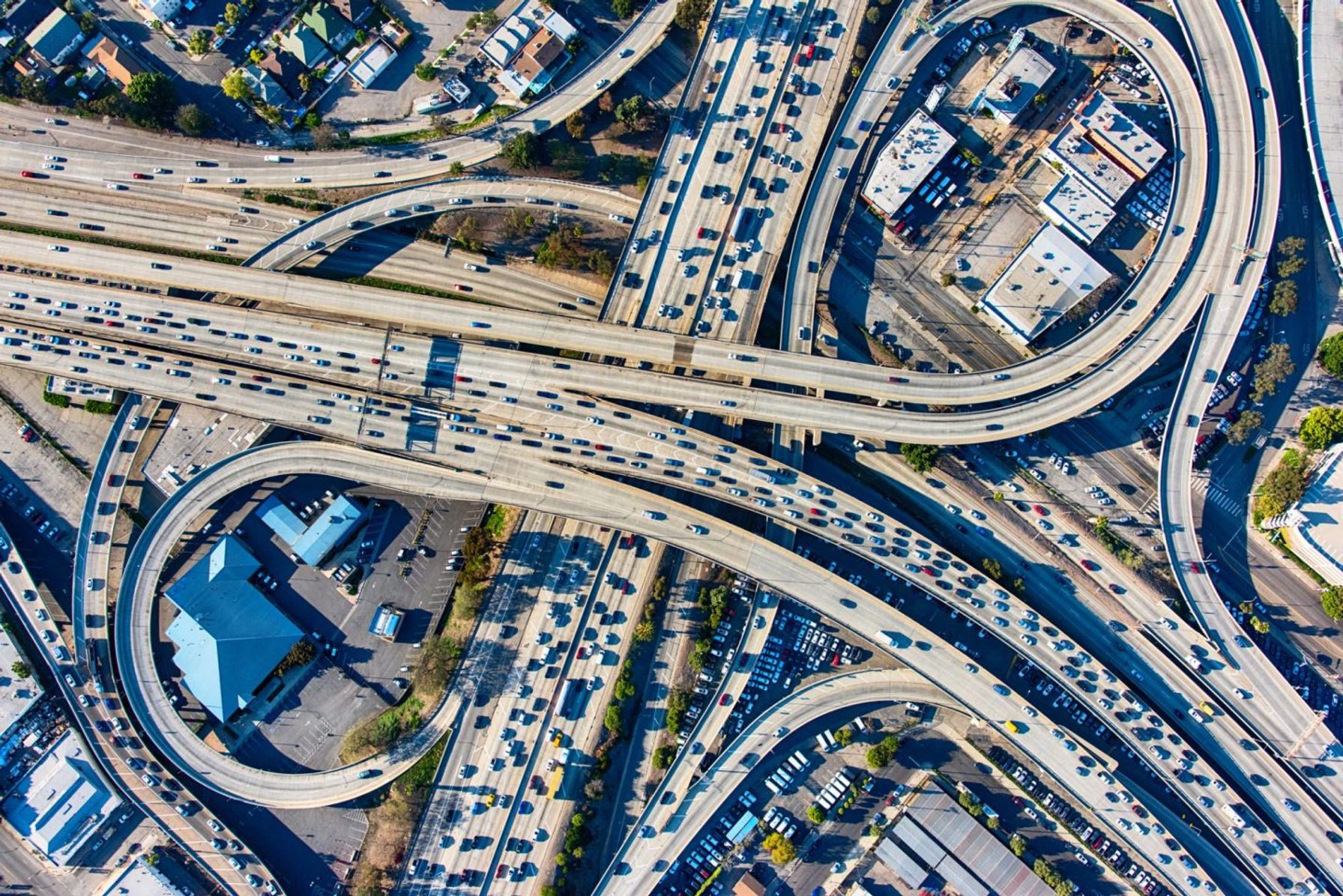
Resources
Infrastructure Solutions
Covering all the bases from project feasibility studies and consultation to engineering and design to construction.
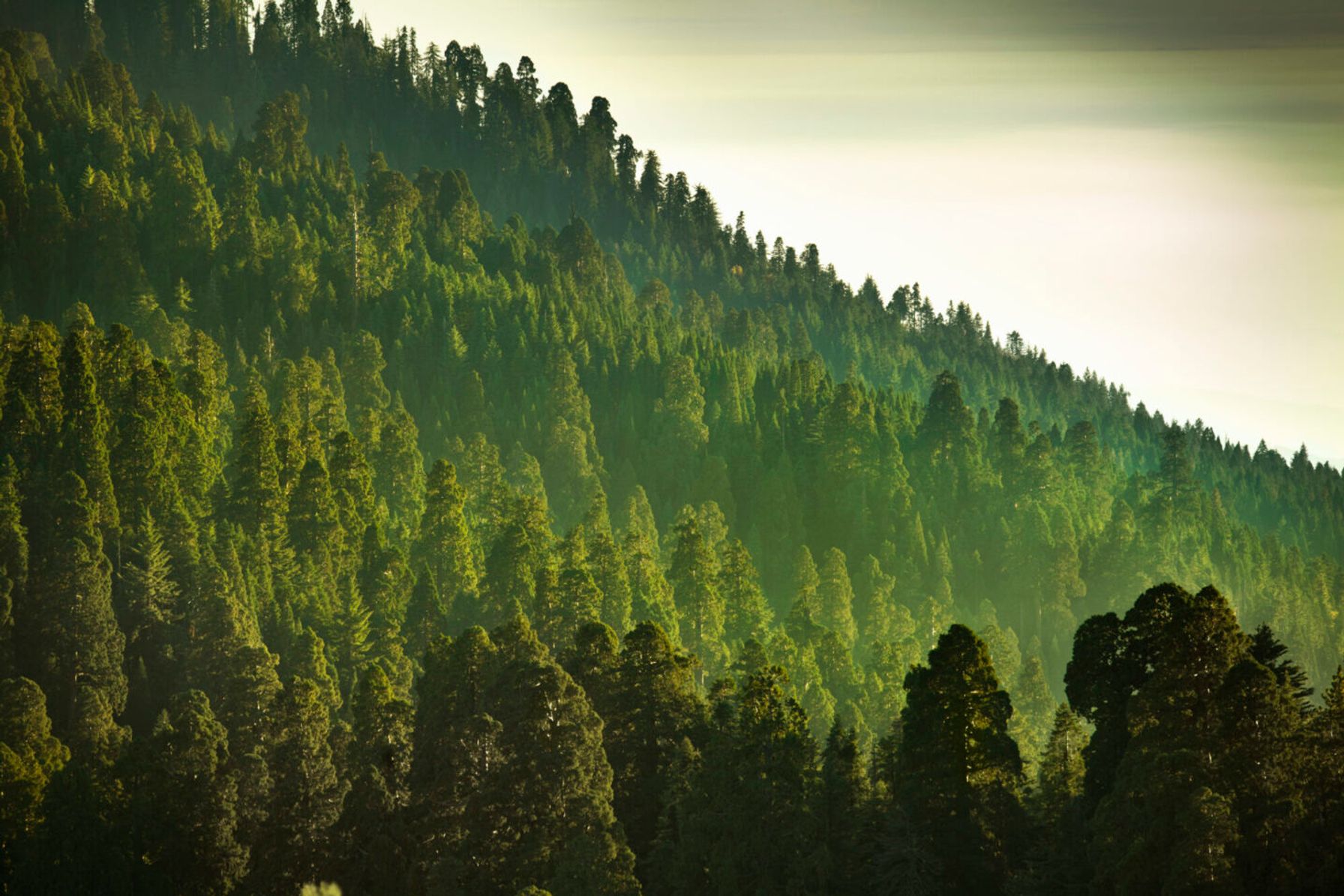
CORE
Technical Resources
Insights About Common Industry Challenges and Solutions
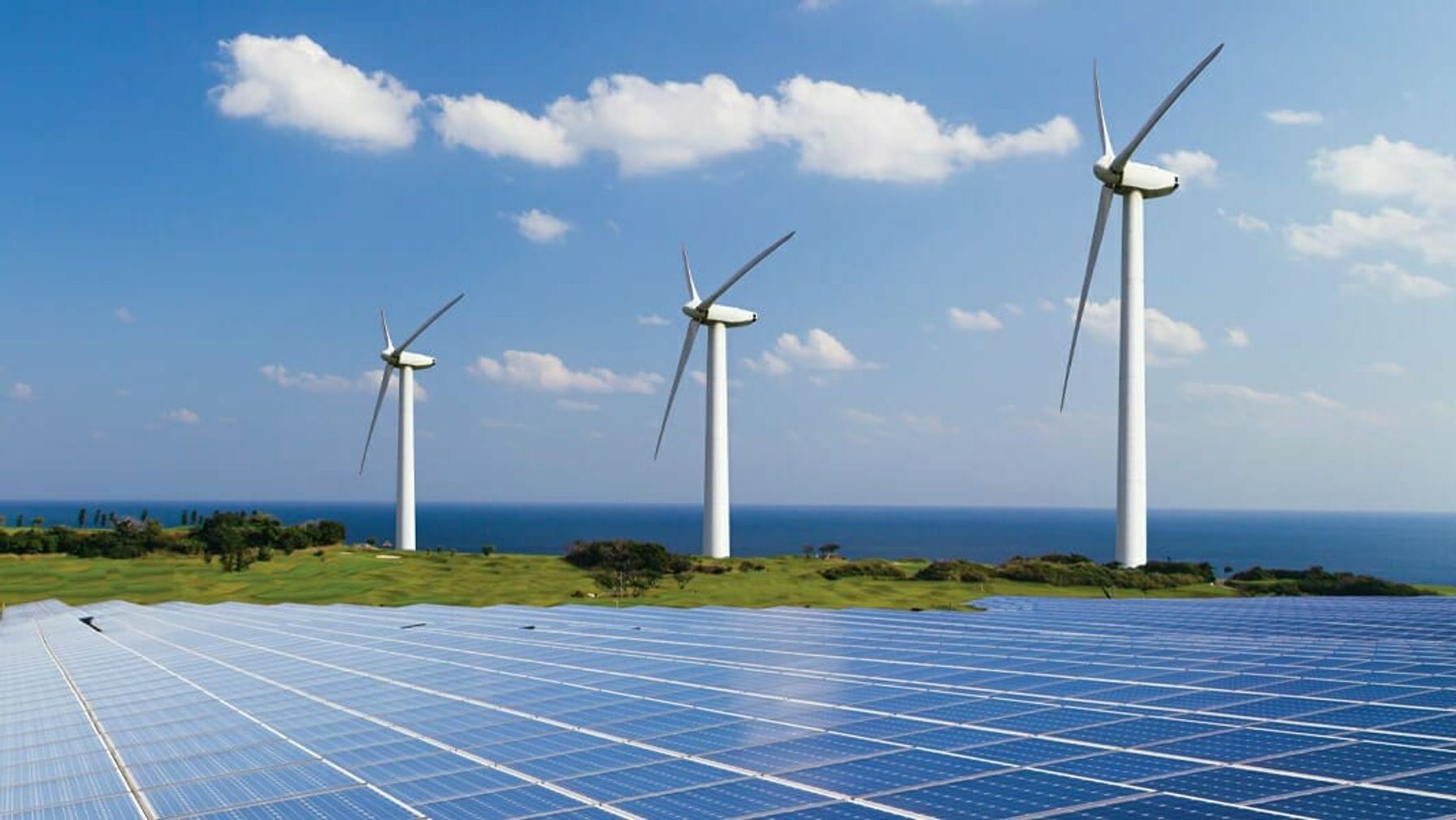
RENEWABLES
Renewable Energy Development
Integrated environmental, engineering and construction solutions for optimal project efficiency and accountability.
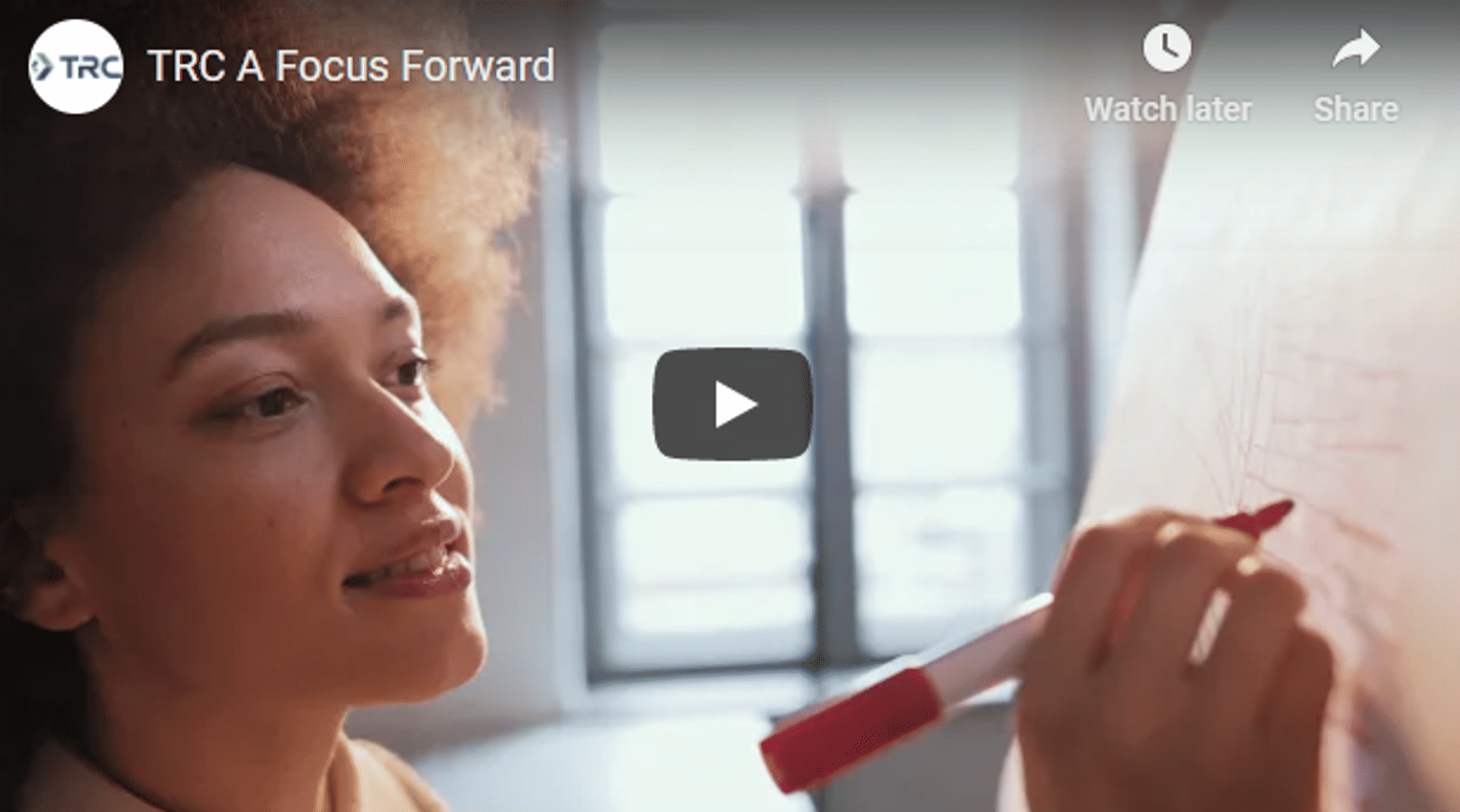
A focus forward.
As the world continues to advance, you need a partner that's advancing ahead of it. Day after day, project after project, TRC helps our clients design, power, connect and fuel the world forward.
Looking for effective solutions to your problems?
Turn to the experts at TRC.